Table of Content
While manufactured homes are one-story designs, a modular home can be of any size. Both manufactured and modular homes look like any other conventionally built home in appearance and both are built to codes that ensure a safe and sound investment. The module will be wrapped and protected for shipping before being load on the truck.

Rather than making plaster walls on-site, they found that it would be easier to mass-produce drywall in a factory. Factory-built homes can also leverage the buying power of large quantities of quality construction materials, resulting in greater savings on your new home when compared to the cost of a stick-built home. Assembly line construction means frequent inspections and opportunity for good oversight of workmanship at every stage.
Early 1900’s: Early Rise and Fall of Modular Homes
If you’re in the market to purchase a home, or considering building one, you may be aware that modular homes are a popular option. Simply put, modular homes have sections that are built in a factory, rather than being fully built on a home site. These parts are then transported to the site and assembled by a builder. Modern standard homes are evolving within the previous few years to the purpose that they’ll vie with ancient stick-built houses somehow. Quality levels and adherence to native building codes have multiplied.
The installation of the plumbing pipes placed on the floor start before the walls are erected but the plumbing works continue on until the plumbing installation is complete once the whole volume is assembled . The pipes will be pressure and leakage tested and to ensure the plumbing installation is completely ready since the only plumbing work left to complete on site is the connection to the public lines. Finding the right modular home loan doesn’t have to be a struggle, and being able to compare qualified lenders has never been easier. We make it simple for you to find the right lender who will help you and your family with modular home financing. The CE mark is a construction norm that guarantees the user of mechanical resistance and strength of the structure. It is a label given by European community empowered authorities for end-to-end process mastering and traceability.
What Does a Modular Home Cost?
PMC modules can be integrated into site built projects or stand alone and can be delivered with MEP, fixtures and interior finishes. Some US courts have ruled that zoning restrictions applicable to mobile homes do not apply to modular homes since modular homes are designed to have a permanent foundation. In Australia, manufactured home parks are governed by additional legislation that does not apply to permanent modular homes. Possible developments in equivalence between modular and site-built housing types for the purposes of real estate appraisals, financing and zoning may increase the sales of modular homes over time. The most important zones that manufacturers have to take into consideration are local wind, heat, and snow load zones. For example, homes built for final assembly in a hurricane-prone, earthquake or flooding area may include additional bracing to meet local building codes.
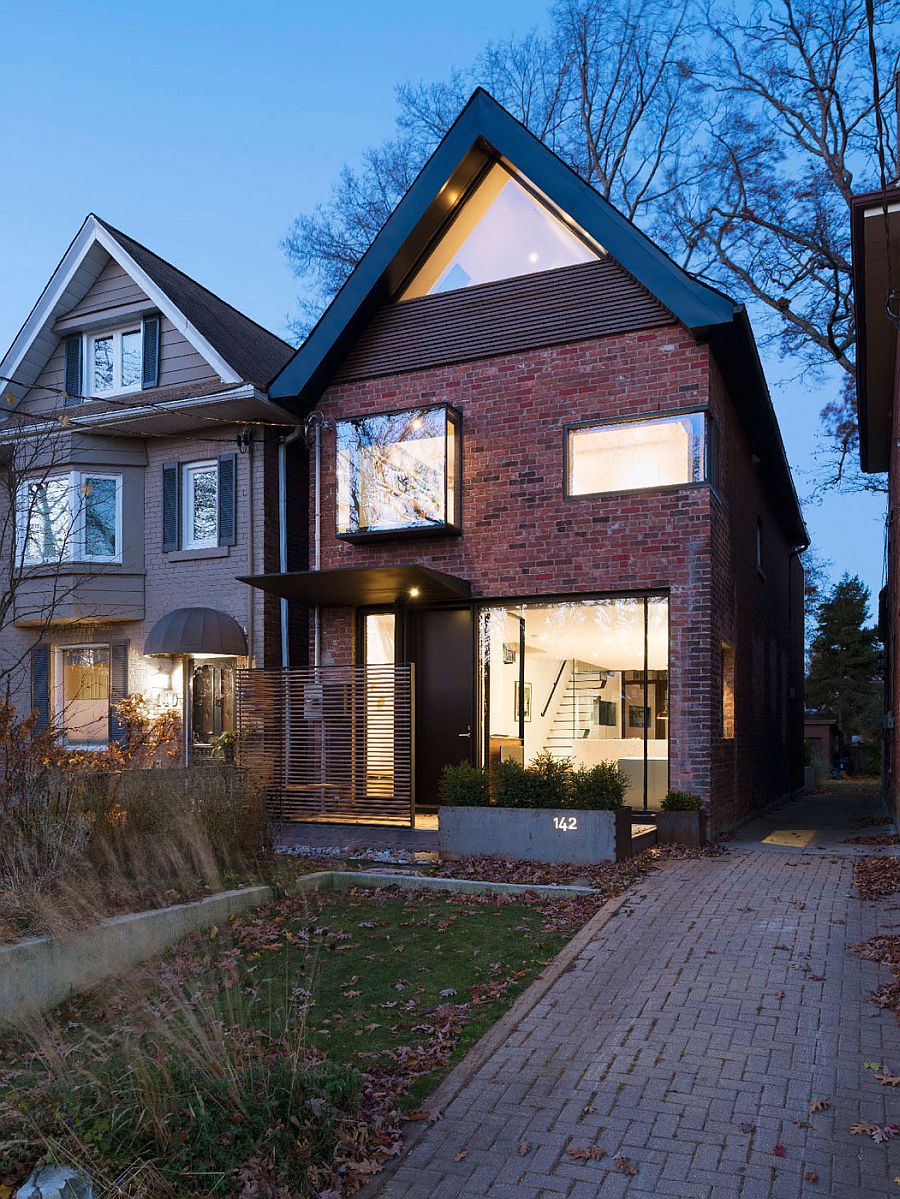
There are also many people who still confuse manufactured homes and modular homes. Manufactured homes, previously known as mobile homes, are built on steel frames called chasses and they cannot be removed. The chasses are used to support the homes and transport them to their permanent locations.
CLASP (Consortium of Local Authorities Special Programme)
Modular homes – also often known as factory-built, prefabricated, or systems-built homes – still only represent about 1.5% of all single family homes in the U.S. But more and more, the interest in modular housing is growing among American homebuyers. This is because modular homes offer both the flexibility to modify and create custom floor plans, as well as all the modern amenities, features, and design styles you’d expect in traditional homes. Our modular buildings are built to the same building codes as traditional site-built construction. Our structures can be placed on a variety of foundations, such as crawlspaces, pilings, or stilts. Affinity Building Systems is based in Lakeland, Georgia and provides modular buildings to independent, authorized builders throughout the Southeast.
Modular homes should also not be confused with manufactured homes , which are built entirely in a factory, then transported in one piece. Once the module is fully finished from inside out, it is time to thoroughly clean it and prepare it for delivery. Once the frame elements are built and ready, it is time to assemble it all together. The walls that have been until now lying horizontally on the floor will be raised, erected and placed on the flooring deck. The walls will be properly fastened and secured to ensure a safe module frame. The assembling of the roof will take place later on in the process since leaving the walls open on the top eases the work.
Modular Home Financing Has Never Been Easier
Prone to strong storms and tornado conditions, modular construction offers the ability to better withstand these storm patterns than its site built counterpart. The inter-module attachments that must be made when assembling a modular home on a foundation offer an inherently stronger home than site built construction can offer. Interior finishes on both the walls and ceilings are typically textured. Corners on interior walls are typically rounded and finish trim around windows is optional. Because of the wider road and lower population density, modules can be as wide as 20' and as long as 90'. The ability to provide larger modules reduces the amount of modules needed to complete a home.

We are here for you, and you can count on us starting with your first phone call or visit. Novi Home Show to Include 5 New Manufactured Homes The Novi Home Show, Oct. 11-13, will include five new, fully-decorated manufactured homes from some of... Manufactured homes use interior wall paneling or drywall, and the exterior typically is composed of prefinished aluminum siding with baked-on enamel treatment. However, as is the case with many of the structural materials and most of the finishing materials, you can exercise your personal preferences. Just as you can request granite countertops, a request can be made to use vinyl or wood composite exterior siding. Another huge change is that these homes are no longer purchased via catalog.
You can check out all of these modular home manufacturer’s floor plans from the central search tool on Commodore’s website. Like other leading modular home manufacturers, part of the appeal of Impresa Modular is the fast and efficient timeline for building your new home. In fact, the company was featured on DIY Network’s "Breakneck Builds" television series in 2015. From start to finish, your custom Impresa home can be built, delivered, and finished in just three to five months. By building in controlled environments, Affinity Building Systems can construct in a much more efficient manner, while not at the mercy of weather and other delays. Our manufacturing facility is housed over 2 ½ acres and is contained on our private 13-acre complex.
Modular homes offer a degree of customization and durability not typically seen in the traditional home-building process. In this blog post, we’ll explore the differences between mobile and modular homes to help you better understand which one works best for your lifestyle needs. Modular construction allows for the building and the site work to be completed simultaneously. According to some materials, this can reduce the overall completion schedule by as much as 50%.
No comments:
Post a Comment